Top 5 Applications of Injection Molding in Manufacturing
By:Admin
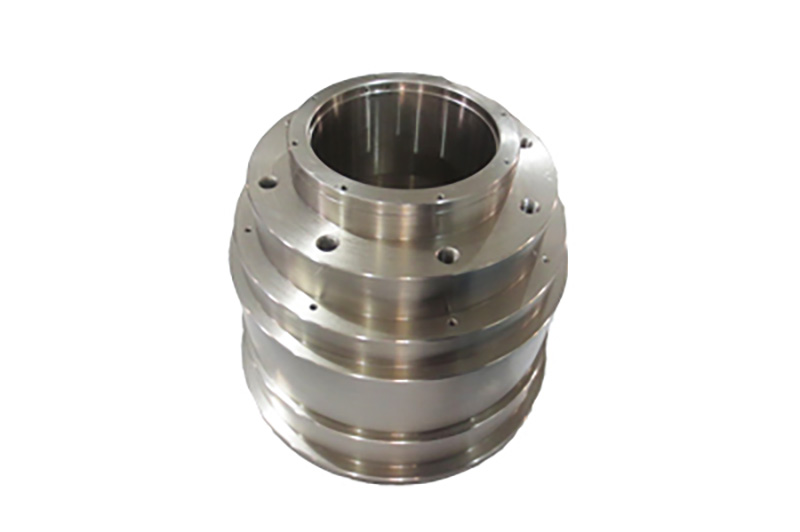
In today's fast-paced world, manufacturers are constantly seeking new and innovative ways to improve their production processes. One such method that has been gaining widespread attention is injection molding. This advanced manufacturing technique has the potential to bring about revolutionary changes in the way products are designed and produced.
Injection molding is a manufacturing process for producing parts by injecting molten material into a mold. It is commonly used for manufacturing a variety of products, including plastic parts, components for medical devices, automotive parts, and consumer goods. This process has gained popularity due to its ability to produce complex and intricate parts with high precision and consistency.
One company that has been at the forefront of utilizing injection molding technology is {} (). The company, established in 1990, has carved a niche for itself in the manufacturing industry by providing high-quality injection-molded parts for a wide range of applications. With a state-of-the-art facility equipped with the latest injection molding machines and a team of experienced engineers, {} is able to deliver custom solutions to meet the unique needs of its clients.
{} is committed to staying ahead of the curve in the ever-evolving manufacturing landscape. With a focus on innovation and customer satisfaction, the company has continually invested in advanced technologies to enhance its production capabilities. This forward-thinking approach has not only enabled {} to maintain its competitive edge but has also positioned the company as a leader in the injection molding industry.
One of the key advantages of injection molding is its ability to produce parts with exceptional precision and accuracy. The process allows for the creation of intricate designs and complex geometries that would be challenging to achieve using traditional manufacturing methods. With the use of computer-aided design (CAD) software and advanced mold-making techniques, {} is able to manufacture high-quality parts with tight tolerances, ensuring superior performance and functionality.
Another advantage of injection molding is its cost-effectiveness. The ability to produce large volumes of parts with minimal waste makes this manufacturing process highly efficient. {} has leveraged this advantage to offer competitive pricing to its customers, making it an attractive choice for businesses looking to streamline their production processes and reduce overall costs.
Furthermore, injection molding is a versatile process that can accommodate a wide range of materials, including thermoplastics, thermosets, and elastomers. This flexibility allows {} to cater to diverse industry needs, from automotive and aerospace to medical and consumer products. By working closely with its customers, the company is able to recommend the most suitable materials for their specific applications, ensuring optimal performance and durability.
In addition to its technical capabilities, {} is dedicated to sustainability and environmental responsibility. The company strives to minimize its environmental impact by implementing eco-friendly practices in its manufacturing processes. By using recyclable materials and optimizing energy consumption, {} is committed to promoting a greener and more sustainable future for the manufacturing industry.
With its dedication to quality, innovation, and customer satisfaction, {} is poised to continue making significant contributions to the advancement of injection molding technology. As the manufacturing landscape continues to evolve, this company remains committed to staying ahead of the curve and delivering cutting-edge solutions to its clients.
In conclusion, injection molding is a game-changer in the manufacturing industry, and {} is leading the charge in harnessing its potential. With its state-of-the-art facilities, technical expertise, and commitment to excellence, {} is well-positioned to continue driving revolutionary changes in the production of high-quality, precision-engineered parts. As the demand for complex and customized products continues to grow, injection molding is likely to play an even more prominent role in shaping the future of manufacturing.
Company News & Blog
Learn About Injection Overmolding: What It Is and How It Works
Injection Overmolding: Revolutionizing Plastic ManufacturingIn today's fast-paced and ever-changing world, the demand for high-quality, innovative products is at an all-time high. As a result, manufacturers are continually seeking new and efficient ways to produce top-of-the-line goods that meet the needs and expectations of consumers. One of the latest developments in the field of plastic manufacturing is Injection Overmolding.Injection Overmolding is a cutting-edge process that involves the injection of molten plastic over a pre-formed substrate or insert. This unique method allows for the creation of complex and multi-material parts, resulting in durable, high-performance products. The process begins with the production of a pre-formed component, which serves as the substrate for the overmolding. This component is then placed within a mold cavity, and molten plastic is injected to encapsulate and bond with the pre-formed substrate, creating a seamless and integrated final product.This advanced manufacturing technique offers a wide range of benefits, including improved product durability, enhanced design flexibility, and reduced production costs. Furthermore, Injection Overmolding allows for the integration of multiple materials, such as rubber, metal, and plastic, resulting in parts with superior functionality and performance.One company at the forefront of Injection Overmolding is {}. With a strong commitment to innovation and excellence, {} has become a leader in the field, providing high-quality overmolding solutions to a diverse range of industries, including automotive, electronics, healthcare, and consumer goods.The company's state-of-the-art facilities and cutting-edge technology enable {} to deliver superior overmolding solutions that meet the specific needs and requirements of their clients. From prototype development to full-scale production, {} offers a comprehensive range of services, including design assistance, material selection, and custom tooling, ensuring that each project is tailored to the unique specifications of the customer.With a team of experienced engineers and technicians, {} has the expertise and capabilities to tackle even the most challenging overmolding projects. The company's relentless pursuit of excellence and continuous investment in research and development have positioned {} as a trusted partner for businesses seeking high-quality, innovative overmolding solutions.In addition to its advanced manufacturing capabilities, {} is also committed to sustainability and environmental responsibility. By utilizing efficient production processes and eco-friendly materials, the company strives to minimize its environmental footprint while delivering top-tier products to its customers. With a focus on innovation, quality, and sustainability, {} is paving the way for the future of plastic manufacturing.As the demand for high-performance, multi-material products continues to grow, Injection Overmolding is poised to revolutionize the plastic manufacturing industry. With its ability to create durable, complex, and integrated parts, Injection Overmolding offers a solution that meets the evolving needs of today's consumers and businesses.In conclusion, Injection Overmolding represents the next frontier in plastic manufacturing, and companies like {} are leading the charge in delivering innovative overmolding solutions to a wide range of industries. With its advanced technology, commitment to excellence, and dedication to sustainability, {} is well-positioned to shape the future of plastic manufacturing and continue to meet the evolving needs of its customers.
Premium CNC Machining for Steel: Unlocking Precision and Efficiency
[News Title:]Steel CNC Machining Revolutionizes Precision Manufacturing with Cutting-Edge Processes[News Introduction:]In today's rapidly evolving world, precision manufacturing is becoming increasingly essential across various industries. One company that has caught the attention of experts and industry leaders worldwide has revolutionized the field with their exceptional steel CNC machining capabilities. Catering to diverse sectors such as automotive, aerospace, and electronics, this innovative company has managed to carve a niche for itself through its advanced processes, delivering unparalleled precision and efficiency. By harnessing the power of steel CNC machining, they have managed to streamline manufacturing processes and redefine the possibilities of precision engineering.[News Body:]The company (company name), a frontrunner in steel CNC machining, prides itself on its state-of-the-art facilities, cutting-edge technology, and a team of highly skilled engineers and machinists. Their commitment to quality and excellence has enabled them to secure a reputation as one of the leading providers of precision machining services worldwide.With steel CNC machining, this company expertly transforms raw materials into complex and intricate components used across a wide range of industries. By utilizing state-of-the-art computer numerical control (CNC) machines and a superior understanding of the properties of steel, they are capable of producing highly accurate and precise parts in a fraction of the time it would take traditional manufacturing methods.One of the key advantages of steel CNC machining lies in its ability to cater to a myriad of design specifications. This technique allows for the production of intricate, high-quality components with tight tolerances, ensuring a perfect fit for various applications. From gears and shafts to brackets and housings, their CNC machines are capable of creating parts that conform to the most demanding requirements.Moreover, the company's cutting-edge software and 3D modeling capabilities enable them to optimize designs and create custom components with unparalleled accuracy and efficiency. This ensures that the final product not only meets but exceeds the client's expectations, making steel CNC machining the ideal choice for industries that demand excellence.In addition to their superior manufacturing capabilities, the company takes pride in its commitment to quality control. With stringent quality checks at every stage of the machining process, they ensure that all components leaving their facilities meet the highest standards. Through the effective use of advanced inspection tools and techniques, they guarantee that each part is flawless, free from defects, and ready for immediate integration into the client's assembly line.The versatility of steel CNC machining also plays a significant role in its widespread adoption across multiple industries. From automotive manufacturing, where precision-engineered parts ensure optimal performance and safety, to aerospace applications, where stringent standards and requirements are paramount, (company name) has consistently delivered exceptional results. Their ability to work with a wide range of steel alloys further enhances their capabilities, allowing them to cater to the specific needs of each client.Going beyond traditional manufacturing, the company's research and development team remains at the forefront of technological advancements. By actively exploring new techniques and materials, they continually refine their processes to deliver even greater precision and efficiency. As industry demands evolve, this commitment to innovation ensures that the company remains a trusted partner for businesses seeking cutting-edge solutions.[News Conclusion:]As the field of precision manufacturing continues to advance, the importance of steel CNC machining cannot be understated. The processes and capabilities offered by (company name) have positioned them as a leader in the industry. With their commitment to quality, expertise, and constant innovation, they are poised to drive forward the next generation of precision components. From helping automotive manufacturers achieve superior performance to aiding aerospace engineers in pushing the boundaries of exploration, steel CNC machining continues to redefine what is possible in precision manufacturing.
Exploring the Limitations of Sand Casting: Factors Hindering the Process
Title: Exploring Sand Casting Disadvantages in the Manufacturing IndustryIntroduction:In the realm of manufacturing, sand casting has long been a traditional and widely-used technique for creating intricate and durable metal components. Many companies, including {}, have successfully employed sand casting in their production processes. However, it is important to be aware of the disadvantages associated with this method in order to make informed decisions in the manufacturing industry.Sand Casting and its Application:Before delving into the drawbacks, it is crucial to understand the fundamentals of sand casting. The process involves pouring molten metal into a sand mold to create a desired shape. This method offers flexibility, affordability, and the ability to produce intricate components with various alloys. Sand casting is widely used in industries like automotive, aerospace, and construction, where complex parts are required.Disadvantage 1: Limited Surface Finish and Precision:One of the major shortcomings of sand casting is the limitation it presents in achieving high surface finish and precision. The texture of the sand mold often transfers inconsistencies onto the final product, resulting in a rougher surface finish. Moreover, the molding process may introduce slight variations in dimensions, making it challenging to achieve precise measurements and tight tolerances. These factors can be critical in industries where the aesthetics and precision of components are paramount, such as consumer electronics and medical devices.Disadvantage 2: Time and Labor Intensive:Sand casting is a time and labor-intensive process, which can significantly impact the overall production timeline and costs. Preparing the molds, including pattern creation, gating system design, and mold assembly, requires skilled labor and careful execution. Additionally, molten metal must be cooled and solidified in the mold, followed by the removal of excess sand and finishing operations. Addressing these steps can be time-consuming, leading to longer lead times and reduced efficiency, especially for industries characterized by high-volume production demands.Disadvantage 3: Limited Complexity and Assembly Integration:While sand casting is suitable for various complex shapes, it has limitations in terms of intricate designs and integration with assembly components. The mold's internal cavities can be challenging to achieve with precision, prohibiting the creation of intricate features. Furthermore, sand casting may not be ideal for components requiring internal passageways, such as cooling channels, as the removal of the sand mold can be difficult and may compromise the final product's integrity. For industries that heavily rely on intricate designs and integration, such as semiconductor manufacturing or advanced machinery, alternative production methods like precision machining may be preferred.Disadvantage 4: Material Waste and Environmental Concerns:Sand casting generates a significant amount of waste material. After each casting, sand molds become unusable and are discarded, contributing to environmental concerns. Additionally, the process can consume large quantities of sand, leading to mining activities and the depletion of natural resources. Companies like {} have been actively working towards sustainable solutions by implementing recycling processes and exploring environmentally-friendly alternatives to sand molds, such as 3D-printed molds or investment casting.Conclusion:Sand casting undeniably plays a crucial role in the manufacturing industry, with its affordability and flexibility making it an attractive choice for many companies, including {}. However, it is essential to be aware of its disadvantages, which include limited surface finish and precision, time and labor intensiveness, limited complexity and integration, and environmental concerns. By understanding these drawbacks, manufacturers can make more informed decisions when choosing their production methods, potentially optimizing their processes and meeting the demands of their respective industries while considering sustainability needs.
Expert Guide to 3-Axis CNC Machining: What You Need to Know
{[Company Name] is proud to announce that it has recently invested in state-of-the-art 3 axis CNC machining technology. This investment will allow the company to enhance its manufacturing capabilities and provide more precise and efficient services to its customers.3 axis CNC machining is a cutting-edge technology that enables high-precision manufacturing of various components and parts. The technology utilizes computer numerical control (CNC) to automate the machining process, resulting in superior accuracy and repeatability. This makes it an ideal solution for a wide range of industries, including aerospace, automotive, medical, and more.With the addition of 3 axis CNC machining, [Company Name] will be able to expand its manufacturing capabilities and offer new product lines to its customers. This technology will enable the company to produce complex and intricate components with ease, allowing for greater design flexibility and faster turnaround times.In addition to enhancing its manufacturing capabilities, [Company Name] is also committed to maintaining the highest quality standards. The company takes pride in ensuring that all products meet or exceed industry regulations and customer specifications. With 3 axis CNC machining, [Company Name] will be able to further guarantee the precision and quality of its products, setting a new standard for excellence in the industry.Moreover, [Company Name] has always been dedicated to continuous improvement and technological innovation. By investing in the latest 3 axis CNC machining technology, the company is demonstrating its commitment to staying at the forefront of industry advancements. This will not only benefit the company and its customers, but also contribute to the overall advancement of manufacturing technology.Furthermore, the investment in 3 axis CNC machining technology demonstrates [Company Name]'s dedication to sustainability and efficiency. The technology allows for the optimization of material usage and reduction of waste, contributing to a more environmentally friendly manufacturing process. This aligns with the company's values and commitment to responsible and sustainable business practices.In conclusion, the addition of 3 axis CNC machining technology is a significant milestone for [Company Name]. It represents the company's dedication to providing the highest quality products and services to its customers, as well as its commitment to innovation and sustainability. With this new technology, [Company Name] is poised to elevate its manufacturing capabilities and set new industry standards for precision and efficiency.Stay tuned for more updates as [Company Name] continues to leverage the latest advancements in technology to deliver unparalleled solutions to its customers.About [Company Name]:[Company Name] is a leading manufacturing company that specializes in providing high-quality components and parts to a diverse range of industries. With a focus on precision, quality, and innovation, the company is dedicated to meeting the unique needs of its customers and delivering exceptional products and services. [Company Name] is committed to continuous improvement and invests in cutting-edge technologies to ensure that it remains at the forefront of industry advancements.
Get the Latest Rapid Prototype Machining Services for Your Business
Rapid Prototype Machining, also known as rapid prototyping, is a cutting-edge technology that is revolutionizing the manufacturing industry. This innovative process allows companies to quickly and efficiently create prototypes of their products, enabling them to test and refine their designs before moving into full-scale production. With the use of advanced computer-aided design (CAD) software and state-of-the-art machining equipment, companies can now turn their ideas into tangible prototypes in a matter of days, rather than weeks or months.One company that is at the forefront of rapid prototype machining is {}. With a history of 25 years in the manufacturing industry, {} has established itself as a leader in the field of precision engineering and machining. Their expertise in working with a wide range of materials, including metals, plastics, and composites, has made them a trusted partner for companies looking to bring their innovative ideas to life.The rapid prototype machining process begins with the creation of a 3D CAD model of the product. This digital design is then used to program the machining equipment, which uses cutting-edge technology such as computer numerical control (CNC) to precisely shape the raw materials into the desired form. The result is a high-quality prototype that accurately represents the final product, allowing companies to test and validate their designs before investing in full-scale production.One of the key advantages of rapid prototype machining is the ability to quickly iterate and refine designs. In traditional manufacturing processes, making changes to a product design can be time-consuming and costly. With rapid prototyping, on the other hand, companies can make modifications to their designs with minimal lead time, allowing them to quickly address any issues and improve the final product.Another benefit of rapid prototype machining is the ability to test the functionality and performance of a product before investing in mass production. By creating a prototype that closely resembles the final product, companies can conduct rigorous testing to ensure that the design meets performance requirements and user expectations. This can help to prevent costly mistakes and rework down the line, ultimately saving time and resources in the long run.In addition to its applications in product development, rapid prototype machining also plays a key role in the creation of custom tooling and fixtures for manufacturing processes. By using rapid prototyping to create custom tooling, companies can reduce lead times and costs associated with traditional tooling methods, while also benefiting from the ability to iterate and refine the tooling design as needed.As a leading provider of precision machining services, {} is committed to staying at the forefront of technological advances in the industry. Their investment in state-of-the-art equipment and ongoing training for their team of skilled engineers and machinists has positioned them as a go-to partner for companies seeking rapid prototype machining services.In addition to their rapid prototype machining capabilities, {} offers a range of other precision engineering services, including CNC milling, turning, grinding, and EDM. Their expertise in working with a broad spectrum of materials and complex geometries has made them a trusted partner for companies in industries such as aerospace, automotive, medical devices, and consumer electronics.The team at {} is dedicated to partnering with their clients to bring their ideas to life. From the initial concept to the final product, they work closely with their customers to ensure that their designs are realized with the highest level of precision and quality. With their advanced capabilities in rapid prototype machining and precision engineering, {} is well-positioned to continue driving innovation in the manufacturing industry for years to come.
Understanding the Steps Involved in the Milling Process
[Company Name] Revolutionizes the Milling Process, Enhancing Efficiency and Quality[City, Date] - [Company Name], a leading innovator in the manufacturing industry, is making waves with its revolutionary milling process. By incorporating cutting-edge technology and advanced techniques, the company has accomplished remarkable improvements in efficiency and quality, setting new industry standards.The milling process is a crucial step in the manufacturing of various products, ranging from automotive components to consumer electronics. Traditionally, this process involves removing material from a workpiece using a rotating cutting tool. However, [Company Name] has taken this fundamental concept to new heights.With a focus on innovation, [Company Name] has developed a state-of-the-art milling process that surpasses traditional methods in terms of speed and precision. By leveraging advanced computer algorithms and artificial intelligence, the company has optimized the milling parameters to ensure the perfect balance between material removal and preservation.One key aspect of [Company Name]'s milling process is the integration of advanced sensors and monitoring systems. These sensors provide real-time feedback on crucial variables such as cutting forces, temperatures, and tool wear. By constantly monitoring these parameters, [Company Name] can make precise adjustments to the milling process, ensuring optimal performance and preventing any potential faults or errors.Additionally, [Company Name] has pioneered an intelligent tooling system that further enhances the efficiency of the milling process. This system utilizes smart tools equipped with sensors to continuously collect data during the machining operation. This data is then analyzed by sophisticated algorithms, allowing for predictive maintenance and precise tool life management. As a result, downtime due to unexpected tool failures is significantly reduced, leading to increased productivity and cost savings.Furthermore, [Company Name] has prioritized sustainability in its milling process. By implementing eco-friendly cutting fluids and optimizing the chip evacuation process, the company has minimized waste and reduced environmental impact. This commitment to sustainability aligns with [Company Name]'s corporate values and resonates with environmentally conscious clients.In terms of quality control, [Company Name] has introduced advanced inspection systems that guarantee the highest level of precision and accuracy. Through the utilization of non-contact measurement technologies, such as laser scanners and optical systems, the company can perform detailed inspections on complex components, ensuring conformity to the tightest tolerances.Customer satisfaction is paramount for [Company Name], and as such, the company provides comprehensive support throughout the milling process. Their team of highly skilled engineers assists clients in selecting the appropriate milling strategies and tools for their specific needs. Additionally, [Company Name] offers training programs and workshops to ensure that operators are well-equipped to utilize the milling process to its full potential.The impact of [Company Name]'s milling process is already being felt across a wide range of industries. Customers have praised the enhanced productivity, improved part quality, and reduced lead times resulting from the adoption of this innovative technology. Numerous companies have reported significant cost savings and increased competitiveness as a direct result of partnering with [Company Name].Looking towards the future, [Company Name] remains committed to pushing the boundaries of milling technology. Through ongoing research and development efforts, the company strives to introduce even more advanced milling techniques that will revolutionize the manufacturing industry once again.In conclusion, [Company Name]'s revolutionary milling process has transformed traditional machining into a high-tech, efficient, and sustainable practice. By seamlessly integrating cutting-edge technology and advanced techniques, the company has set a new industry standard for milling, driving productivity, quality, and cost-effectiveness to unparalleled heights.
Enhance Your Precision with a 3-Axis Milling Machine
Title: Advanced 3-Axis Milling Machine Revolutionizes Precision ManufacturingIntroduction:In the ever-evolving landscape of precision manufacturing, companies are constantly on the lookout for cutting-edge technologies that can significantly enhance their efficiency and product quality. Keeping up with this demand, a leading manufacturing tool supplier has recently launched a groundbreaking 3-axis milling machine designed to streamline production processes and maximize precision at every step. By integrating state-of-the-art features and advanced capabilities, this new milling machine is set to revolutionize precision manufacturing and propel businesses to new heights.Cutting-Edge Features and Functionality:The newly introduced 3-axis milling machine combines cutting-edge technology with years of manufacturing expertise to offer unrivaled precision and efficiency. The machine's robust design, incorporating high-quality materials and components, ensures reliable and consistent performance throughout its life cycle. Equipped with an advanced computer numerical control (CNC) system, this milling machine provides unparalleled accuracy and repeatability, allowing manufacturers to achieve their desired results with minimal errors or rework.The machine's 3-axis configuration allows for precise and simultaneous control over the X, Y, and Z axes, providing manufacturers with the flexibility to create intricate and complex components with ease. Its high-speed spindle rotation capability ensures rapid material removal, reducing machining time and increasing productivity. Additionally, its generous work envelope enables the milling of large-sized workpieces, catering to a wide range of manufacturing applications.Enhanced User Experience:Understanding the importance of user-friendly interfaces in modern manufacturing, the 3-axis milling machine incorporates an intuitive control panel that simplifies operation for both seasoned professionals and novice operators. Featuring a user-friendly graphical interface, the machine allows operators to easily input their desired specifications, monitor machining processes in real-time, and make any necessary adjustments on the fly.Furthermore, the milling machine's software offers a comprehensive range of programmable functions, enabling users to automate repetitive tasks and optimize workflows. This harmonious blend of cutting-edge hardware and intuitive software empowers manufacturers to significantly reduce human error, increase production output, and enhance overall operational efficiency.Unrivaled Precision and Quality Assurance:Precision is at the heart of this 3-axis milling machine, as it is equipped with precision ball screws and linear guides that facilitate smooth and accurate movements along all three axes. This ensures that each milling operation is executed with the utmost precision, resulting in exceptional component quality and dimensional accuracy. Furthermore, the machine's advanced probing system allows for in-process measurements, enabling operators to verify the integrity of machined components and make necessary adjustments in real-time.Wide Range of Applications:The versatility of the 3-axis milling machine makes it suitable for a diverse range of industries and applications. From aerospace and automotive to medical device manufacturing, this revolutionary machine can effortlessly handle various materials, including metals, composites, plastics, and more. Its ability to cut, carve, drill, and shape intricate components guarantees that manufacturers can meet the unique demands of their respective industries with exceptional efficiency and accuracy.Conclusion:The introduction of this advanced 3-axis milling machine marks a significant milestone in the realm of precision manufacturing. Its cutting-edge features, intuitive user interface, and unrivaled precision empower manufacturers to streamline their production processes, reduce errors, and elevate their product quality to new heights. With this revolutionary machine, businesses can gain a competitive edge in the demanding world of precision manufacturing, allowing for accelerated growth and enhanced customer satisfaction.
Top 5 CNC Milling Lathes for Precision Engineering
In today's fast-paced and demanding industrial environment, precision and efficiency are key factors in staying competitive. This is where the CNC milling lathe from {} comes into play. With its advanced technology and superior performance, this innovative machine is transforming the way companies produce and manufacture their products. Let's take a closer look at how this CNC milling lathe is revolutionizing the industry.{} has been a leading provider of advanced manufacturing solutions for over two decades. The company's commitment to innovation and excellence has earned them a reputation for delivering cutting-edge technology to their clients. Their CNC milling lathe is a testament to their dedication to pushing the boundaries of what is possible in the manufacturing world.This CNC milling lathe is equipped with state-of-the-art features that set it apart from traditional milling machines. Its precision engineering allows for incredibly tight tolerances and flawless surface finishes, ensuring that every part produced is of the highest quality. The machine's high-speed capabilities and multi-axis functionality also enable complex and intricate parts to be manufactured with ease and efficiency. This level of precision and speed is unparalleled in the industry and has significantly enhanced the productivity of companies that have implemented this technology into their operations.One of the standout features of this CNC milling lathe is its user-friendly interface and intuitive programming capabilities. This allows operators to easily input complex designs and geometries, simplifying the manufacturing process and reducing the margin for error. Additionally, the machine's automation and self-monitoring capabilities minimize downtime and optimize production, making it a valuable asset for any company looking to streamline their manufacturing processes.Furthermore, {} has a team of experienced engineers and technical support staff who are dedicated to providing exceptional service and assistance to their clients. From installation and training to ongoing maintenance and support, {} ensures that their customers are fully equipped to harness the full potential of their CNC milling lathe. This level of support and expertise sets {} apart from its competitors and has made them a trusted partner for companies looking to invest in advanced manufacturing technology.The impact of this CNC milling lathe on the industry has been significant. Companies that have integrated this technology into their operations have reported substantial improvements in their production processes. The machine's ability to produce high-precision components with minimal lead time has allowed companies to meet the growing demands of their customers while maintaining the highest standards of quality. This has not only enhanced their competitiveness in the market but has also opened up new opportunities for growth and expansion.In conclusion, the CNC milling lathe from {} is a game-changer in the manufacturing industry. Its advanced technology, precision engineering, and user-friendly interface have set a new standard for efficiency and quality in production processes. With {}'s commitment to providing exceptional service and support, companies have a reliable partner to help them navigate the complexities of integrating this innovative technology into their operations. As the industry continues to evolve, it is clear that the CNC milling lathe from {} will play a pivotal role in shaping the future of manufacturing.
Top Tips for Constructing a CNC Machine
The construction of a new CNC machine has been completed at {}. This state-of-the-art machine is expected to enhance the company's production capabilities and contribute to its overall growth and success in the industry. With an extensive focus on precision, efficiency, and quality, this new addition signifies a significant milestone for the company.CNC (Computer Numerical Control) machines play a crucial role in modern manufacturing processes by automating the production of intricate and complex parts. These machines are widely used in various industries, including automotive, aerospace, healthcare, and electronics, to name a few. With the ability to precisely fabricate components from a wide range of materials such as metals, plastics, and composites, CNC machines have revolutionized the way products are manufactured.The newly constructed CNC machine at {} is equipped with the latest technology and features, making it a valuable asset for the company. Its high-speed machining capabilities, coupled with advanced tooling and cutting-edge software, enable it to produce parts with exceptional accuracy and repeatability. This level of precision is essential for meeting the stringent quality standards demanded by the company's clientele.Additionally, the machine boasts a large working envelope, allowing it to accommodate a diverse range of part sizes and geometries. This versatility is a significant advantage for the company, as it expands its capacity to handle a broader spectrum of projects and customer requirements. Whether it's prototyping, small-batch production, or large-scale manufacturing, this CNC machine is poised to deliver optimal results across the board.The construction of this new CNC machine aligns with {}'s commitment to staying at the forefront of technological advancements in manufacturing. By investing in state-of-the-art equipment, the company aims to enhance its competitiveness in the market and position itself as a leading provider of precision-engineered components and assemblies. The decision to add this machine to its production floor reflects the company's dedication to meeting the evolving needs of its customers while maintaining the highest standards of quality and innovation.Furthermore, the introduction of the new CNC machine is expected to have a positive impact on the company's overall efficiency and productivity. With its ability to automate and streamline manufacturing processes, the machine will contribute to reducing lead times and increasing throughput. This not only benefits {}'s internal operations but also translates to enhanced service for its customers, enabling prompt delivery of orders without compromising on quality.In addition to its operational advantages, the new CNC machine underscores {}'s ongoing commitment to sustainability and environmental responsibility. By leveraging advanced technologies that optimize material usage and minimize waste, the company continues to demonstrate its dedication to eco-friendly manufacturing practices. This aligns with its broader mission to operate in a manner that respects the environment and supports a sustainable future for generations to come.As {} celebrates the completion of its new CNC machine construction, the company looks forward to the opportunities and growth it will bring. With a strong foundation built on innovation, precision, and excellence, the company is poised to leverage this new addition to further elevate its capabilities and deliver exceptional value to its customers. The investment in this cutting-edge technology is a testament to {}'s enduring pursuit of manufacturing excellence and its unwavering dedication to staying ahead of the curve in an ever-evolving industry.
Unlocking the Secrets of the Innovative Insert Molding Process
[Title]: Innovative Insert Molding Process Enhances Manufacturing Efficiency[Subtitle]: Taking Manufacturing Precision to New Heights[Date]: [Insert Date][City], [State] - In their relentless pursuit of excellence, [Company Name], a leading manufacturer in the industry, has introduced an innovative insert molding process that promises to revolutionize the manufacturing landscape. This groundbreaking technique has allowed the company to enhance efficiency and precision, cementing their position as pioneers in the field.[Company Name], with their rich history of delivering cutting-edge solutions, has consistently demonstrated their commitment to pushing the boundaries of what is possible. By successfully implementing the insert molding process, they aim to revolutionize the way manufacturing operations are conducted.The insert molding process revolutionizes manufacturing by combining multiple materials or components into a single molded plastic part. This process greatly reduces assembly steps and enhances productivity, streamlining the entire manufacturing process. By eliminating the need for separate components and multiple assembly lines, [Company Name] has significantly reduced production time, allowing them to meet the increasing demands of their customers.Through the innovative use of the insert molding process, [Company Name] has successfully eliminated the need for additional assembly steps, thereby reducing costs and minimizing the margin for error. This not only translates into significant time and cost savings but also ensures a higher degree of quality control and consistency in the final product.Unlike traditional manufacturing techniques, the insert molding process involves the encapsulation of specific components or inserts within the molded plastic part. This creates a strong bond between the plastic and the inserted components, resulting in a durable and reliable end product. This advanced manufacturing technique has been widely hailed as a game-changer, enabling manufacturers to produce complex and compact parts with unmatched precision and reliability.[Company Name]'s mastery of the insert molding process stems from their in-depth understanding of the industry and their continuous investment in cutting-edge technologies. By leveraging their expertise and state-of-the-art facilities, they have succeeded in refining this process to deliver superior quality products to their clients.Furthermore, the insert molding process offers numerous design possibilities, enabling manufacturers to create products that are aesthetically pleasing while maintaining functionality. By seamlessly integrating various materials and components, manufacturers can achieve a more sophisticated and versatile end product.[Company Name] has always been at the forefront of innovation and has earned a reputation for delivering outstanding customer satisfaction. By adopting the insert molding process, they have cemented their position as pioneers in the industry, offering their clients a comprehensive range of solutions that cater to their diverse requirements.The benefits of the insert molding process extend beyond just manufacturing efficiency. By reducing the number of components and assembly steps, [Company Name] has also contributed to a greener and more sustainable industry. The decreased material usage and lower energy consumption associated with this manufacturing technique result in a reduced carbon footprint.[Company Name] takes pride in their dedication to continuous improvement. They constantly strive to push the boundaries of what is possible, and the introduction of the insert molding process is a testament to their relentless pursuit of excellence. This innovation has not only redefined their position in the industry but also set new standards for manufacturing precision and efficiency.In conclusion, [Company Name]'s introduction of the insert molding process has revolutionized the manufacturing landscape. By combining multiple materials or components into one molded plastic part, they have enhanced efficiency, reduced production time, and improved the overall quality of their products. This groundbreaking technique is a testament to the company's commitment to innovation and customer satisfaction. As [Company Name] continues to lead the way in cutting-edge solutions, the future of manufacturing looks brighter than ever.