CNC Machining Aluminum Parts: Precision Engineering at its Finest
By:Admin
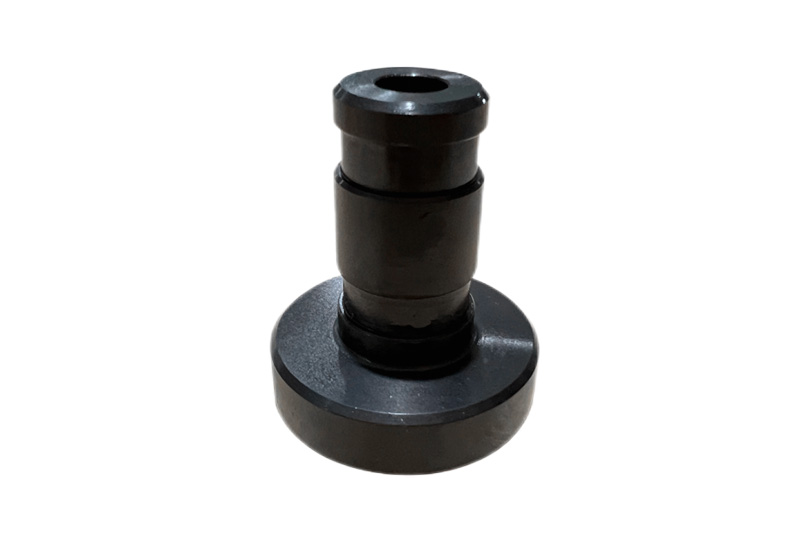
Introduction:
In an ever-evolving manufacturing landscape, one company has emerged as a pioneer in delivering cutting-edge solutions - [Company Name]. With a reputation for excellence and a commitment to technological advancements, [Company Name] has recently unveiled their latest innovation - CNC Machining Aluminum Parts. This state-of-the-art development is set to revolutionize the precision engineering industry, providing companies worldwide with unparalleled accuracy and efficiency in their manufacturing processes.
Unveiling CNC Machining Aluminum Parts:
[Company Name] is proud to introduce its latest offering, CNC Machining Aluminum Parts, which are designed and engineered to meet the demands of today's modern manufacturing requirements. With a strong emphasis on precision, reliability, and quality, these parts are poised to surpass industry standards.
Utilizing the latest Computer Numerical Control (CNC) technology, [Company Name]'s CNC Machining Aluminum Parts offer exceptional accuracy, consistency, and repeatability. This cutting-edge technology enables the production of complex and intricate designs with incredible precision, leaving no room for human error.
Applications and Benefits:
The versatility of [Company Name]'s CNC Machining Aluminum Parts makes them suitable for a wide range of applications across various industries. From automotive and aerospace to electronics and medical equipment, these parts are designed to meet the specific needs of each sector.
One of the key advantages of CNC Machining Aluminum Parts is their exceptional material properties. Aluminum, known for its lightweight yet durable characteristics, is a popular choice for manufacturers seeking to enhance performance without compromising structural integrity. The CNC machining process further enhances this by ensuring precise dimensions, tight tolerances, and a superior surface finish.
Additionally, CNC Machining Aluminum Parts offer greater design flexibility, allowing manufacturers to create customized components tailored to their exact specifications. This level of customization, coupled with the precision offered by CNC machining, ensures a high degree of accuracy and functionality in the final product.
Another noteworthy benefit is the time and cost savings that CNC Machining Aluminum Parts offer. The automated nature of the CNC machining process enables faster and more efficient production, reducing lead times and allowing for increased productivity. This efficiency translates into cost savings for manufacturers, ultimately leading to enhanced profitability and a competitive edge in the global market.
Quality Control and Assurance:
[Company Name]'s commitment to quality is a cornerstone of their success. Before being shipped to customers, every CNC Machining Aluminum Part undergoes rigorous testing and inspection to ensure compliance with the highest quality standards. This comprehensive quality control process guarantees that only flawless parts are delivered, further enhancing customer satisfaction and maintaining [Company Name]'s reputation as a reliable industry leader.
Future Prospects:
With the unveiling of CNC Machining Aluminum Parts, [Company Name] solidifies its position as a forward-thinking manufacturer, continually adapting to industry changes and exceeding customer expectations. This innovation acts as a stepping stone to further advancements, enabling [Company Name] to explore new possibilities and expand its range of precision-engineered products.
Conclusion:
[Company Name]'s introduction of CNC Machining Aluminum Parts marks a significant milestone in the manufacturing industry. By offering unmatched precision, superior quality, and cost-efficiency, these cutting-edge parts contribute to the overall advancement of various sectors, driving innovation and competitiveness. As [Company Name] continues to prioritize technological advancements and customer satisfaction, it is clear that their commitment to excellence will propel them to new heights within the global manufacturing industry.
Company News & Blog
Understanding the Steps Involved in the Milling Process
[Company Name] Revolutionizes the Milling Process, Enhancing Efficiency and Quality[City, Date] - [Company Name], a leading innovator in the manufacturing industry, is making waves with its revolutionary milling process. By incorporating cutting-edge technology and advanced techniques, the company has accomplished remarkable improvements in efficiency and quality, setting new industry standards.The milling process is a crucial step in the manufacturing of various products, ranging from automotive components to consumer electronics. Traditionally, this process involves removing material from a workpiece using a rotating cutting tool. However, [Company Name] has taken this fundamental concept to new heights.With a focus on innovation, [Company Name] has developed a state-of-the-art milling process that surpasses traditional methods in terms of speed and precision. By leveraging advanced computer algorithms and artificial intelligence, the company has optimized the milling parameters to ensure the perfect balance between material removal and preservation.One key aspect of [Company Name]'s milling process is the integration of advanced sensors and monitoring systems. These sensors provide real-time feedback on crucial variables such as cutting forces, temperatures, and tool wear. By constantly monitoring these parameters, [Company Name] can make precise adjustments to the milling process, ensuring optimal performance and preventing any potential faults or errors.Additionally, [Company Name] has pioneered an intelligent tooling system that further enhances the efficiency of the milling process. This system utilizes smart tools equipped with sensors to continuously collect data during the machining operation. This data is then analyzed by sophisticated algorithms, allowing for predictive maintenance and precise tool life management. As a result, downtime due to unexpected tool failures is significantly reduced, leading to increased productivity and cost savings.Furthermore, [Company Name] has prioritized sustainability in its milling process. By implementing eco-friendly cutting fluids and optimizing the chip evacuation process, the company has minimized waste and reduced environmental impact. This commitment to sustainability aligns with [Company Name]'s corporate values and resonates with environmentally conscious clients.In terms of quality control, [Company Name] has introduced advanced inspection systems that guarantee the highest level of precision and accuracy. Through the utilization of non-contact measurement technologies, such as laser scanners and optical systems, the company can perform detailed inspections on complex components, ensuring conformity to the tightest tolerances.Customer satisfaction is paramount for [Company Name], and as such, the company provides comprehensive support throughout the milling process. Their team of highly skilled engineers assists clients in selecting the appropriate milling strategies and tools for their specific needs. Additionally, [Company Name] offers training programs and workshops to ensure that operators are well-equipped to utilize the milling process to its full potential.The impact of [Company Name]'s milling process is already being felt across a wide range of industries. Customers have praised the enhanced productivity, improved part quality, and reduced lead times resulting from the adoption of this innovative technology. Numerous companies have reported significant cost savings and increased competitiveness as a direct result of partnering with [Company Name].Looking towards the future, [Company Name] remains committed to pushing the boundaries of milling technology. Through ongoing research and development efforts, the company strives to introduce even more advanced milling techniques that will revolutionize the manufacturing industry once again.In conclusion, [Company Name]'s revolutionary milling process has transformed traditional machining into a high-tech, efficient, and sustainable practice. By seamlessly integrating cutting-edge technology and advanced techniques, the company has set a new industry standard for milling, driving productivity, quality, and cost-effectiveness to unparalleled heights.
Unlocking the Power of 4-Axis CNC Milling: Exploring Advanced Machining Capabilities
Title: Enhancing Precision and Productivity with Advanced 4-Axis CNC Milling TechnologyIntroduction:In a rapidly evolving manufacturing landscape, companies across industries are constantly seeking innovative solutions to maximize precision and productivity. One such advancement that has garnered significant attention is the incorporation of 4-axis CNC milling technology. This cutting-edge technique allows for the creation of intricately designed parts and components with unparalleled precision, efficiency, and versatility. Today, we delve into the world of 4-axis CNC milling, exploring its remarkable capabilities and the ways in which it revolutionizes the manufacturing process, propelling industries into a new era of growth and competitiveness.Revolutionizing Manufacturing with 4-Axis CNC Milling:Traditionally, milling was a manual process that involved removing material from a workpiece with rotary cutters. However, with the advent of computer numerical control (CNC) machining, the process has been completely transformed. CNC milling utilizes pre-programmed computer software instructions that precisely control cutter movement and material removal, resulting in consistent and accurate machining operations. While 3-axis CNC milling has served the industry well, the incorporation of a fourth axis significantly expands the capabilities of this technology.The 4th axis, often referred to as the A-axis, enables the milling cutter to rotate around the X-axis, allowing for the creation of complex geometries and the machining of undercuts, bevels, and other intricate features. This added versatility opens up a myriad of possibilities for manufacturers, facilitating the production of more complex and aesthetically appealing components.Enhanced Precision and Efficiency:With 4-axis CNC milling, manufacturers can achieve unparalleled precision and accuracy. The rotational capabilities of the A-axis enable the machine to approach the workpiece from various angles, reducing the need for multiple setups. This not only saves time but also minimizes errors associated with manual repositioning. The result is faster production cycles, improved part quality, and reduced scrap rates, ultimately leading to increased cost-effectiveness and customer satisfaction.Furthermore, 4-axis CNC milling technology excels in machining complex curves, contours, and profiles, ensuring consistency across multiple parts. With the ability to perform intricate operations in a single setup, manufacturers can accelerate production while maintaining the highest level of precision, meeting the demands of even the most intricate designs.Versatility Across Industries:The applications of 4-axis CNC milling span a wide range of industries, benefiting from its inherent precision and flexibility. In the aerospace sector, this technology is instrumental in the production of engine components, turbine blades, and aircraft structural parts, which require intricate machining and strict adherence to tolerances. Similarly, in the automotive industry, companies utilize 4-axis CNC milling for machining engine blocks, cylinder heads, and transmission components.Medical practitioners also rely on 4-axis CNC milling to fabricate complex dental implants, prosthetics, and surgical instruments. The versatility of 4-axis CNC milling technology allows manufacturers to cater to the evolving needs of various industries, providing customized solutions that meet the highest standards of quality and precision.Conclusion:As industries continue to push the boundaries of innovation, the integration of 4-axis CNC milling technology has become an increasingly vital aspect of the manufacturing process. The enhanced precision, efficiency, and versatility offered by this cutting-edge technology propel industries to new heights, ensuring accelerated production cycles, improved part quality, and increased customer satisfaction. With its ability to machine intricate geometries and complex designs, 4-axis CNC milling paves the way for the future of precision manufacturing, revolutionizing industries and strengthening their competitive edge in the global market.
Revolutionizing Precision Machining: Unveiling the Power of Plastic CNC
Plastic CNC Provider Revolutionizes Manufacturing with Cutting-Edge TechnologyIn an era where manufacturing excellence and efficiency are highly prized, Plastic CNC, a leading provider of precision plastic machining solutions, has emerged as a game-changer in the industry. With their commitment to innovation and advanced technology, the company has established itself as a trusted partner for businesses seeking high-quality plastic components and parts.Since its inception, Plastic CNC has been at the forefront of revolutionizing the manufacturing process through their state-of-the-art machinery, skilled workforce, and dedication to customer satisfaction. Specializing in computer numerical control (CNC) machining, the company utilizes automated systems to precisely shape and mold plastic into intricate components with exceptional accuracy and consistency.Plastic CNC's commitment to technological innovation is evident through their extensive range of cutting-edge CNC machines. These machines are designed to handle various types of plastics, including but not limited to acrylic, polycarbonate, nylon, and polyethylene. The company's vast repertoire of machinery ensures that they can cater to the diverse needs and specifications of their clients, regardless of the complexity or intricacy of the desired components.One of the key advantages that sets Plastic CNC apart from its competitors is its dedicated team of highly skilled engineers and technicians. These professionals possess a deep understanding of the intricacies of plastic machining and are adept at leveraging the capabilities of their advanced machinery. Their expertise allows Plastic CNC to consistently deliver products of unmatched precision and quality, with tight tolerances and smooth finishes exceeding industry standards.Plastic CNC's commitment to customer satisfaction is reflected in their ability to handle projects of varying sizes and complexities. From prototyping and small-scale production runs to large-scale manufacturing projects, the company has the capability and capacity to accommodate the unique needs and timelines of their clients. Their advanced CNC machines and streamlined production processes ensure prompt delivery of products without compromising on quality.Furthermore, Plastic CNC's dedication to sustainability is commendable. By employing efficient manufacturing processes and optimizing material usage, the company minimizes waste and reduces its environmental footprint. Their commitment to responsible plastic machining aligns with the global efforts to promote sustainable practices in the manufacturing industry.Over the years, Plastic CNC has built a strong reputation among a diverse range of industries due to their unwavering commitment to excellence. The company has successfully served clients in sectors such as electronics, automotive, aerospace, medical, and consumer goods. Their ability to meet the stringent demands of these industries while maintaining competitive pricing has contributed to their long-term success and global reach.To ensure seamless collaboration with their clients, Plastic CNC offers comprehensive design and engineering support. By leveraging computer-aided design (CAD) software and working closely with clients during the initial design phase, the company can optimize the manufacturability of the desired components. This collaborative approach fosters innovation, reduces production costs, and allows for quicker turnaround times.In an evolving landscape where precision and efficiency are critical, Plastic CNC continues to redefine the manufacturing industry. Through its cutting-edge technology, skilled workforce, and customer-centric approach, the company consistently delivers top-notch plastic machining solutions. As they continue to push the boundaries of innovation, Plastic CNC remains a trusted partner for businesses seeking the highest quality plastic components and parts.
Exploring the Benefits and Applications of Cnc Molding in Modern Manufacturing Processes
Title: Revolutionary Cnc Molding Technique Sets New Standards in ManufacturingIntroduction:In an era where innovation and efficiency drive the manufacturing industry, a breakthrough in the form of Cnc Molding technology is emerging as a game-changer. This revolutionary technique promises to reshape the way products are designed, developed, and produced. With its unparalleled precision, speed, and cost-effectiveness, Cnc Molding is poised to set new standards in the manufacturing field.Company Background and Expertise:{Company Name}, a prominent player in the manufacturing industry, has unveiled its cutting-edge Cnc Molding technology. With a rich history spanning several decades, {Company Name} has established itself as a pioneer in delivering excellence and embracing the latest technological advancements. Their expertise in the field, combined with their commitment to driving innovation, has paved the way for this groundbreaking development.Understanding Cnc Molding:Cnc Molding, also known as Computer Numerical Control Molding, is a state-of-the-art manufacturing process that utilizes computer-controlled machines to shape materials into desired forms. Unlike traditional molding techniques, Cnc Molding ensures unparalleled precision, efficiency, and repeatability. By following a digital design prototype, the technology enables manufacturers to produce highly intricate and complex components with utmost accuracy.Benefits of Cnc Molding:1. Enhanced Precision: The integration of computer control systems eliminates the possibility of human error, ensuring precise replication of designs and eliminating defects. This high level of precision ensures product consistency, reducing wastage and overall costs.2. Streamlined Production: Cnc Molding technology dramatically accelerates the production process. With its ability to perform multiple tasks simultaneously, the technology maximizes efficiency and reduces lead times. This streamlining of operations increases productivity, enabling manufacturers to meet market demands promptly.3. Cost-Effectiveness: By minimizing material wastage and requiring fewer human interventions, Cnc Molding significantly reduces production costs. The elimination of manual labor and the use of optimized resources result in improved cost-effectiveness, making it an attractive option for manufacturers across various industries.4. Design Freedom: Cnc Molding empowers designers to create innovative and intricate designs that were previously unachievable. With the ability to produce complex shapes and patterns with ease, this technology unlocks a new realm of possibilities, enabling manufacturers to create unique products that stand out in the market.Applications of Cnc Molding:The applications of Cnc Molding are vast and span across industries such as automotive, aerospace, electronics, medical, and consumer goods. Its usage is particularly prominent in the production of custom parts, prototypes, and intricate components that require high precision.Future Implications:As Cnc Molding continues to evolve, the implications for the manufacturing industry are immense. The integration of artificial intelligence, machine learning, and digital twins creates an even more robust system capable of even greater efficiency and accuracy. The technology's potential for customization and adaptability positions it as a frontrunner in the future of manufacturing.Conclusion:Cnc Molding technology, introduced by {Company Name}, is set to revolutionize the manufacturing industry. With its exceptional precision, streamlined production, cost-effectiveness, and design freedom, it promises to set new standards and transform the way products are made. As it continues to develop, this groundbreaking technology is poised to usher in a new era of manufacturing excellence.
Enhanced Accuracy and Efficiency: Discover the World of Stamping Parts
[News Title]: Precision Stamping Parts Provider Excels in Ensuring Quality and Efficiency in Manufacturing Processes[Date][City, State] - The precision stamping parts industry has seen significant growth in recent years, and one company that has played a key role in this expansion is [Company Name]. As a leading provider of precision stamping parts, the company has continuously delivered high-quality products that meet the evolving needs of various industries. With a commitment to quality, efficiency, and innovation, [Company Name] has established itself as a trusted partner for businesses worldwide.Established in [Year], [Company Name] has been at the forefront of the precision stamping parts industry for over [Number] years. The company's extensive experience and expertise enable it to offer a wide range of precision-stamped components, catering to diverse industries, including automotive, electronics, aerospace, telecommunications, and more.One of the key factors that set [Company Name] apart from its competitors is its unwavering commitment to ensuring the highest level of quality. Every step of the manufacturing process adheres to strict quality control measures, guaranteeing the reliability and durability of the precision stamping parts produced. The company's state-of-the-art facilities are equipped with advanced technology and machinery, enabling precise fabrication and accurate dimensions.In addition to maintaining stringent quality standards, [Company Name] also places great emphasis on maintaining a streamlined and efficient manufacturing process. By leveraging advanced automation and robotics, the company minimizes human error and maximizes productivity. These automated processes not only contribute to the consistency and precision of the parts but also reduce production time, enabling faster delivery to customers.Moreover, [Company Name] recognizes the importance of staying ahead of market trends and investing in research and development. The company boasts a team of highly skilled engineers and technicians who are constantly exploring innovative techniques to enhance the precision and performance of stamped parts. Collaborating closely with clients, [Company Name] ensures that their specific requirements and expectations are met with customized solutions.Catering to the global marketplace, [Company Name] maintains a strong network of clients and partners throughout the world. The company's commitment to excellence has earned it a loyal customer base, with clients relying on its precision stamping parts for their critical applications. With a thorough understanding of international regulations and industry standards, [Company Name] swiftly adapts to varying requirements across different regions, ensuring seamless collaboration.Furthermore, environmental sustainability is a core value at [Company Name]. The company is dedicated to reducing its carbon footprint and optimizing energy efficiency across its operations. By implementing eco-friendly practices and utilizing sustainable materials, [Company Name] remains committed to the economic and environmental well-being of the communities it serves.The success of [Company Name] is testament to its continuous pursuit of excellence, customer-centric approach, and commitment to innovation. By achieving the highest standards of quality and efficiency, the company has secured a leading position in the precision stamping parts industry. As industries evolve and demand for precision components continues to grow, [Company Name] remains poised to meet and exceed the expectations of its diverse clientele.Contact:[Company Name][Address][Phone Number][Email Address][Website]###[Note to Writer: Please proofread the article for grammar, style, and accuracy prior to publishing. Adjust word count if necessary.]
Enhancing Efficiency and Precision: The Ultimate Guide to Machining Fixture Design
Machining Fixture Design: Enhancing Precision and Efficiency in ManufacturingIn today's fast-paced manufacturing industry, precision and efficiency are paramount. Companies are constantly searching for ways to improve their production processes, reduce costs, and enhance product quality. One such solution that has gained significant attention is machining fixture design. By removing brand names, we can focus on the concept itself and explore how this innovative technology is revolutionizing manufacturing.Machining fixtures are specialized tools used to hold and position workpieces during machining operations. They ensure that the workpiece remains stable and secure, minimizing errors and maximizing productivity. By providing a rigid support structure, machining fixtures enable precision machining, resulting in accurate and consistent parts.With advancements in design and engineering, machining fixtures have evolved to cater to the unique requirements of various industries. Whether it is the automotive, aerospace, or electronics sectors, machining fixture design plays a vital role in optimizing the manufacturing process. By customizing the fixtures according to the specific needs of the product, companies can achieve greater flexibility and efficiency.One key factor contributing to the success of machining fixture design is computer-aided design (CAD) software. CAD allows engineers to create highly complex and detailed fixture designs, taking into account factors such as material properties, clamping forces, and geometric constraints. By simulating the machining process in a virtual environment, engineers can identify potential issues and make necessary adjustments before manufacturing the actual fixture. This not only saves time but also reduces the risk of errors, ensuring a seamless production process.Furthermore, the integration of CAD with computer-aided manufacturing (CAM) software allows for a streamlined transition from design to production. The CAM software generates machine instructions directly from the CAD model, enabling the efficient programming of machining operations. This integration promotes collaboration between design and production teams, resulting in better communication, reduced lead times, and improved overall efficiency.In addition to CAD and CAM, the use of advanced materials and technologies has revolutionized machining fixture design. Lightweight and high-strength materials, such as aluminum alloys and carbon fiber reinforced polymers, have replaced traditional materials like steel. These modern materials offer greater rigidity, reducing vibrations during the machining process and improving surface finish quality. Moreover, they contribute to the overall weight reduction of fixtures, making them more ergonomic and easier to handle.In line with the principles of Industry 4.0, machining fixture design has also embraced automation and robotics. Robotic machining fixtures are capable of performing complex tasks with high precision, reducing human errors and dependence. These fixtures can be programmed to adapt to different workpieces, further enhancing flexibility in production processes. By automating repetitive tasks, manufacturers can increase productivity, reduce costs, and improve worker safety.The company, known for its expertise in machining fixture design, has been at the forefront of these advancements. With a dedicated team of engineers and designers, they have consistently pushed the boundaries of innovation in manufacturing. By continually investing in research and development, the company has been able to develop cutting-edge solutions tailored to meet specific customer needs.From the automotive industry to aerospace and beyond, this company's machining fixtures have become synonymous with precision and efficiency. Their commitment to quality and customer satisfaction has made them a trusted partner for numerous manufacturers worldwide. Through their collaborations and partnerships, they aim to further optimize machining processes, driving the industry towards greater productivity and competitiveness.In conclusion, machining fixture design holds tremendous potential for the manufacturing industry. By leveraging the power of CAD, CAM, advanced materials, and automation, companies can enhance precision, improve efficiency, and reduce costs. As this technology continues to evolve, it is expected to play an increasingly integral role in the manufacturing landscape, enabling businesses to stay ahead in the competitive global market.
Creating an Injection Mold: A Step-by-Step Guide
Title: Manufacturing Company Pioneers Effortless Injection Mold Creation ProcessIntroduction:{Company Name}, a leading manufacturing company, is revolutionizing the industry with their innovative approach to creating injection molds. With their cutting-edge technology and commitment to excellence, they are streamlining the production process for numerous industries. The company's recent advancements have paved the way for more efficient and cost-effective mold creation, ensuring faster turnaround times without compromising on quality or precision.Body:1. Introduction to Injection Molds:Injection molds are an essential component in the production of a wide range of plastic and metal parts. These molds are created to meet specific requirements, with intricate designs and precise dimensions. Traditionally, manufacturing injection molds was a time-consuming and costly process, often causing delays and skyrocketing production costs.2. Streamlined Process for Injection Mold Creation:{Company Name} has developed an innovative solution that simplifies the injection mold creation process. By leveraging the latest technologies and expertise, they have reduced the turnaround time while upholding the highest quality standards. Their streamlined process greatly benefits clients from various industries, including automotive, medical, and consumer goods.3. Customization and Design:One of the key features of {Company Name}'s injection mold creation process is its ability to provide customizable designs. They work closely with clients to understand their unique requirements, ensuring that every mold is tailored to their specific needs. The company's team of experts utilizes advanced software and tools to translate clients' ideas into flawless designs, guaranteeing optimal functionality and durability.4. Enhanced Precision and Quality Control:With their state-of-the-art technology and advanced manufacturing techniques, {Company Name} ensures precision to the finest detail in every injection mold they produce. The company's commitment to quality control is evident throughout the entire manufacturing process. Rigorous testing and inspection procedures are implemented to guarantee that each mold meets or exceeds industry standards before it is released to clients.5. Reduced Time and Cost Savings:{Company Name}'s accelerated injection mold creation process significantly reduces the lead time compared to traditional methods. By cutting down on waiting periods and optimizing production efficiency, clients can initiate their manufacturing processes sooner, thereby reducing downtime and costs. This advantage allows businesses to bring their products to market more rapidly, gaining a competitive edge.6. Sustainable Manufacturing Practices:In addition to their commitment to efficiency and quality, {Company Name} is dedicated to sustainable manufacturing practices. The company employs environmentally-friendly materials and processes wherever possible, prioritizing renewable resources and waste reduction. By adopting these practices, they contribute to a greener future while serving the needs of their clients.7. Dedicated Customer Support:{Company Name} prides itself on providing exceptional customer support throughout the mold creation process. Their team of experts collaborates closely with clients, offering guidance and support as needed. From the initial design phase to post-production assistance, the company ensures that clients have a smooth and hassle-free experience, fostering long-term partnerships built on trust and reliability.Conclusion:{Company Name}'s groundbreaking injection mold creation process sets a new standard for the manufacturing industry. Their commitment to precision, quality control, customization, and sustainability is revolutionizing the way molds are produced. With their shorter lead times, cost savings, and dedicated customer support, {Company Name} continues to transform the industry, enabling businesses to thrive in today's fast-paced market while maintaining the highest standards of quality and efficiency.
How to Achieve Successful Overmolding of Plastic onto Metal
Title: A Revolutionary Advancement in Manufacturing: Overmolding Plastic On MetalIntroduction:In a groundbreaking development in the manufacturing industry, a leading company has recently unveiled its latest innovation in overmolding technology, allowing the seamless integration of plastic onto metal components. This cutting-edge process promises to revolutionize various industries, offering unparalleled opportunities for enhanced product durability, design flexibility, and cost-effectiveness. By merging the benefits of metal strength with the versatility of plastic, this groundbreaking technique opens up endless possibilities for manufacturers across the globe. Background:Recognizing the growing demand for more durable and aesthetically appealing products, manufacturers have long been seeking innovative ways to combine the strengths of different materials. These endeavors have led to the evolution of overmolding, a process that involves molding one material, usually plastic, over an existing component made of another material, commonly metal. Overmolding has been widely utilized in various industries, including automotive, electronics, and consumer goods, to improve product performance, ergonomics, and aesthetics.Product Introduction:Leading the charge in this realm of technology-advanced manufacturing is an industry trailblazer known for its commitment to innovation and relentless pursuit of excellence. Through tireless research and development, this company has perfected the art of overmolding plastic on metal, achieving unparalleled precision and quality in their products. The company's breakthrough overmolding process involves the injection of molten plastic onto metal components, resulting in a durable, seamless bond that surpasses traditional plastic or metal components in terms of both strength and aesthetic appeal.Advantages of Overmolding Plastic On Metal:1. Enhanced Durability: Overmolding plastic on metal creates a robust bond that significantly improves the structural integrity of the product. By minimizing the risk of component failure due to impacts, temperature variations, or chemical exposure, manufacturers can ensure longer product lifespans and ultimately enhance customer satisfaction.2. Improved Design Flexibility: Overmolding offers unparalleled design freedom, enabling manufacturers to create complex shapes and innovative designs that were previously not achievable with traditional manufacturing techniques. The ability to combine various materials with different properties allows for the creation of aesthetically pleasing and ergonomically superior products.3. Cost-effectiveness: Overmolding eliminates the need for additional assembly processes, reducing overall production costs. By combining multiple components into a single overmolded part, manufacturers can streamline their manufacturing processes, minimize assembly time, and decrease labor expenses.4. Reduced Noise and Vibration: Overmolding plastic dampens noise and absorbs vibrations, making it an ideal choice for applications requiring noise reduction, such as automotive interiors and consumer goods. This not only enhances user comfort but also improves the overall quality and perceived value of the product.Applications in Various Industries:The introduction of overmolding plastic on metal opens up new possibilities across a wide range of industries:1. Automotive: Overmolded components find extensive use in automotive interiors, offering improved aesthetics, comfort, and functional integration. From steering wheels to gear knobs, the overmolding process allows manufacturers to create visually appealing, ergonomic, and durable components.2. Electronics: Overmolded connectors, switches, and protective casings in the electronics industry provide enhanced resistance to moisture, dust, and impact. This not only improves the product's performance and durability but also enhances user safety.3. Consumer Goods: Overmolding plastic on metal can significantly enhance the quality and functionality of consumer goods. From kitchen appliances to power tools, the incorporation of overmolded components improves ergonomics, reduces noise, and extends product lifespan.Conclusion:The advent of overmolding plastic on metal marks a significant leap forward in manufacturing technology, offering unprecedented opportunities for industries seeking to enhance the durability, design flexibility, and cost-effectiveness of their products. The seamless integration of plastic onto metal components enables manufacturers to create innovative, aesthetically pleasing, and high-performance products that surpass the limits of traditional manufacturing techniques. As this groundbreaking technology continues to evolve, it is poised to revolutionize numerous industries and drive the development of the manufacturing sector to new heights.
The Ultimate Guide to Efficient Cnc Fixture Design for Manufacturing Success
Title: Innovative CNC Fixture Design Revolutionizes Manufacturing ProcessesIntroduction:In a breakthrough development within the manufacturing industry, an innovative CNC fixture design is set to transform production processes, providing greater efficiency, accuracy, and versatility. This cutting-edge technology marks a significant milestone in manufacturing, empowering companies to improve their productivity and competitiveness in the global market.The Company's Vision:Born out of a deep passion for revolutionizing the manufacturing domain, the company behind this groundbreaking CNC fixture design aims to redefine industry norms. Their team of experienced engineers and technicians have dedicated years of research and development to create this state-of-the-art technology, which promises to streamline operations and enhance overall production quality.The CNC Fixture Design:This remarkable CNC fixture design incorporates a myriad of advanced features that address the challenges of traditional fixture designs. It leverages the latest technologies, including adaptive control systems and intelligent sensor integration, to optimize machining processes and improve the overall user experience.One of the key highlights of this fixture design is its modular approach, allowing for versatile application across various production requirements. The ability to quickly adjust and reconfigure the fixture greatly enhances manufacturing flexibility, saving precious time and resources. Furthermore, the design includes built-in error detection mechanisms, minimizing defects and ensuring consistent, high-quality output.Another noteworthy aspect of this CNC fixture design is its emphasis on ergonomics and operator safety. The system integrates user-friendly interfaces, intuitive controls, and enhanced safety features, reducing the risk of accidents and promoting a seamless work environment.Industry Impact:The introduction of this advanced CNC fixture design is poised to revolutionize manufacturing practices across a wide range of industries. From automotive and aerospace to electronics and medical devices, the versatility and adaptability of this technology make it applicable to numerous sectors.The increased efficiency and accuracy offered by this fixture design will open up new possibilities for manufacturers. It allows for more complex and intricate designs, shorter production cycles, and greater cost-effectiveness. Companies can expect to witness significant improvements in product quality, reduced downtime, and enhanced overall profitability.Furthermore, this CNC fixture design aligns with the ongoing industry trend towards automation and digitization. Its integrated smart systems enable seamless data collection, analysis, and real-time adjustments, contributing to improved productivity and competitiveness on a global scale.Future Prospects:The company behind this CNC fixture design remains committed to continuous innovation and technological advancements. They are actively exploring partnerships with manufacturers seeking to enhance their production capabilities. The aim is to collaborate closely with industry leaders to customize and optimize the design according to specific needs, ensuring a seamless integration of this technology into existing processes.Moreover, through ongoing research and development efforts, the company plans to expand the capabilities of the CNC fixture design further. This includes exploring advancements in materials, sensors, and automation, as well as integrating artificial intelligence and machine learning technologies.Conclusion:As the manufacturing industry embraces the era of automation and digitization, this revolutionary CNC fixture design promises to redefine traditional production methods. With its emphasis on efficiency, accuracy, versatility, and safety, this technology will undoubtedly revolutionize manufacturing processes in diverse sectors. As this innovative solution gains momentum, manufacturers can look forward to a new era of optimized productivity, improved product quality, and sustained growth in a highly competitive global market.